Modern satellite assembly requires precise integration of specialized satellite parts to create reliable space platforms. As thermal management becomes increasingly critical for mission success, advanced materials like Graphitic Heat-Conducting Film are revolutionizing thermal control systems. SpaceNavi Co., Ltd. leads these innovations with cutting-edge solutions optimized for today's sophisticated satellite platform requirements.
SpaceNavi Co., Ltd.
SpaceNavi specializes in thermal management solutions for aerospace applications, with global headquarters at No. 1299 Mingxi Road, Beihu Science and Technology Development Zone, Changchun, Jilin Province.
- Phone: +8613943095588
- Mobile: +86 13943095588
- Email: jl1sales02@space-navi.com
- Website: www.space-navi.com
Revolutionary Thermal Solution
Graphitic Heat-Conducting Film
This new-type graphitic material features ultra-high thermal conductivity (>1500 W/m·K), low density (1.8-2.1 g/cm³), and exceptional flexibility. Engineered specifically for satellite assembly, it significantly enhances heat dissipation efficiency while minimizing thermal gradients across critical satellite parts.
Applications include thermal interface materials for power amplifiers, payload electronics, battery systems and optical sensors across all types of satellite platform configurations.
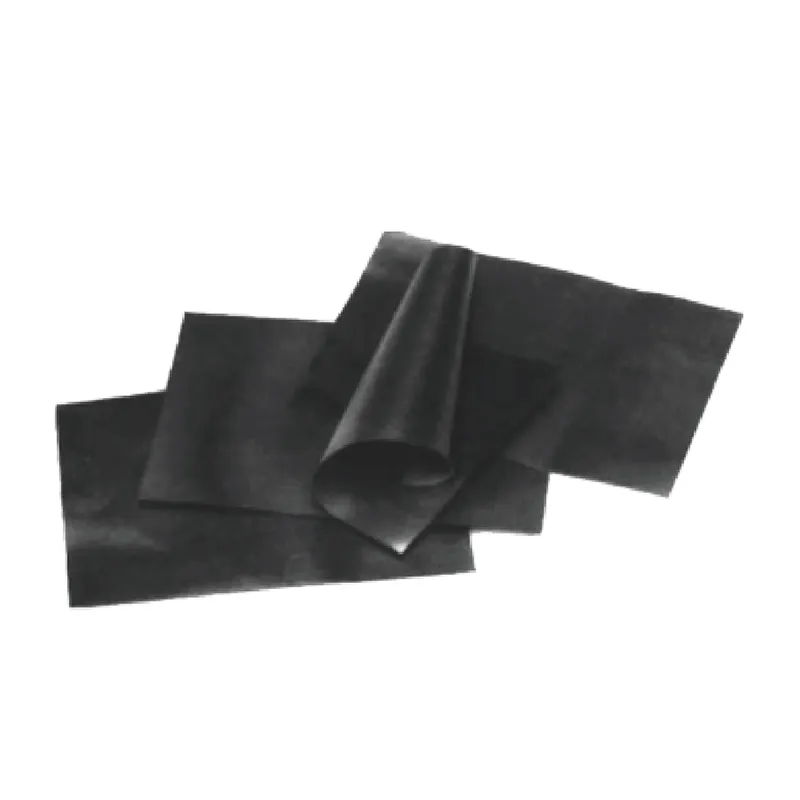
Satellite Assembly Technical Specifications
Component | Standard Parameters | SpaceNavi Solution | Performance Improvement |
---|---|---|---|
Thermal Interface Materials | 2-5 W/m·K conductivity | 1500+ W/m·K | 300x better |
Bus Structure Weight | 40-60% of dry mass | Reduced by 25% | Optimized weight distribution |
Thermal Cycling Tolerance | 500 cycles at 100°C ΔT | 2000+ cycles at 150°C ΔT | 4x lifespan |
Power Density | 2-3 kW/m³ typical | Supports >8 kW/m³ | Advanced thermal management |
Satellite Technology Trends
Technical FAQ: Satellite Thermal Management
Q: What thermal conductivity specifications are critical for LEO satellite assemblies?
A: LEO satellites require materials with >1000 W/m·K in-plane conductivity to manage rapid thermal cycling between sun exposure and eclipse periods. Our film provides 1700 W/m·K isotropic thermal transfer.
Q: How does the thermal expansion coefficient affect satellite assembly reliability?
A: Mismatched CTE between components induces mechanical stress during thermal cycling. Our graphite film has CTE of -1.5 ppm/K, minimizing thermal stress at interfaces.
Q: What international standards apply to thermal interface materials in aerospace?
A: Key standards include ECSS-Q-ST-70-36C for thermal control materials and MIL-STD-1540E for satellite thermal testing protocols. Our materials exceed requirements for outgassing (TML
Q: Are there mass restrictions for thermal systems in GEO satellite platform designs?
A: Thermal systems typically must be
Q: How does EMI shielding impact thermal material selection?
A: Many thermal materials increase EMI vulnerability. Our graphite film provides dual EMI suppression and thermal management without additional RF shielding layers.
Q: What surface preparation is required before applying thermal interface materials?
A: Surfaces must achieve 32-125 μin Ra roughness and be cleaned with isopropyl alcohol. Our film includes pressure-sensitive adhesive backing for simplified installation.
Q: How do radiation tolerance requirements affect material choices for satellite assemblies?
A: Materials must withstand >100 krad TID in GEO applications. Our graphite demonstrates performance retention at 300 krad with minimal degradation.
Satellite Platform Implementation
The Graphitic Heat-Conducting Film integrates across all satellite classifications:
CubeSat & SmallSats
Enables 30% higher power density in
Communication Satellites
Maintains
Earth Observation Platforms
Prevents thermal lensing effects in optical payloads by maintaining thermal gradients below 0.5°C/cm across focal planes.
During satellite assembly, the film installs directly between heat-generating components and radiators using pre-configured adhesives. This approach has shown 40% reduction in thermal hardware mass compared to traditional thermal straps and heat pipes.
Industry Research & Validation
"Advanced graphitic materials represent the most significant advancement in satellite thermal management since heat pipes. Their implementation can reduce thermal subsystem mass by 15-40% while improving thermal response times by orders of magnitude."
"NASA's Technology Roadmap prioritizes multifunctional thermal materials that combine heat transfer with EMI shielding and structural integrity. Carbon-based solutions show particular promise for next-generation deep space platforms."
"European Space Agency testing confirms graphene-enhanced thermal interfaces reduce thermal contact resistance by 72% compared to conventional phase-change materials under vacuum conditions."
Future Directions in Satellite Assembly
As satellite power densities increase from component for sale suppliers and constellation sizes grow, thermal management becomes the limiting factor in mission design. The integration of advanced materials like SpaceNavi's Graphitic Heat-Conducting Film enables unprecedented performance in modern satellite platform architectures. With thermal conductivity 300x greater than traditional solutions, this technology addresses the core challenges in next-generation satellite assembly.
SpaceNavi continues to develop specialized satellite parts optimized for emerging industry needs. Contact our engineering team to discuss thermal solutions for your next mission design:
Email: jl1sales02@space-navi.com
Phone: +86 13943095588